1. Laser Cutting
Laser cutting is a precise and efficient method for shaping metal materials. The process begins with a high-energy laser beam being generated by a laser source. This beam is then focused onto the metal surface through a focusing lens. The intense heat from the laser beam rapidly melts, vaporizes, or burns the metal at the targeted area.
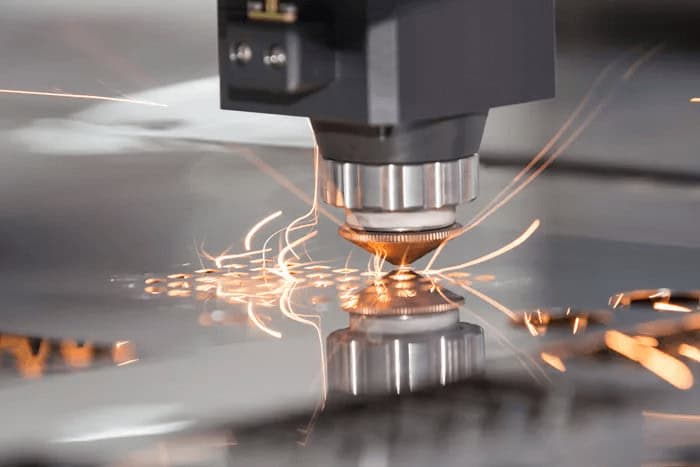
A gas jet is often used simultaneously to blow away the molten or vaporized metal, creating a clean-cut edge. The laser cutting machine is controlled by a computer-numerical-control (CNC) system, which follows a pre-programmed path. This allows for the cutting of complex shapes and patterns with high accuracy, typically achieving tolerances as low as ±0.1mm. The speed of laser cutting depends on factors such as the type and thickness of the metal, laser power, and gas flow rate. For thin sheets of metal, cutting speeds can be quite high, making it suitable for mass production applications.
2. Laser Marking
Laser marking involves using a laser beam to create permanent marks on the metal surface. There are several types of laser marking, including annealing, engraving, and foaming.
In annealing marking, the laser heats the metal surface to a specific temperature, causing a color change due to oxidation. This method is often used for marking serial numbers, barcodes, and logos on metals without altering the surface topography. Engraving, on the other hand, removes a small amount of material from the metal surface by vaporizing it with the laser beam, creating a recessed mark. Foaming marking occurs when the laser causes the metal surface to foam and form a raised mark.
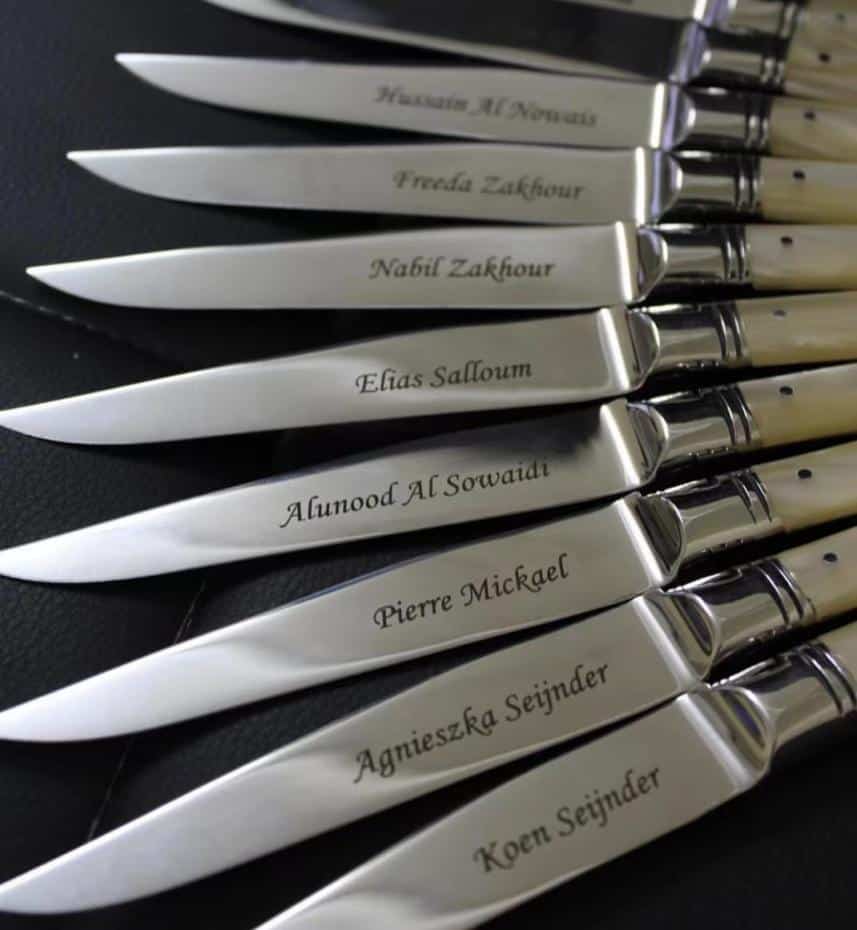
The process is highly precise and can create marks with very fine details. It is non-contact, which means there is no physical wear on the marking tool, and it can be easily automated for high-volume production. The laser marking system is also very flexible, allowing for quick changes in marking content and design.
3. Laser Welding
Laser welding is a technique that joins two or more metal parts together using a laser beam as the heat source. The laser beam is focused on the joint area, melting the metal and fusing the parts. There are two main types of laser welding: conduction welding and keyhole welding.
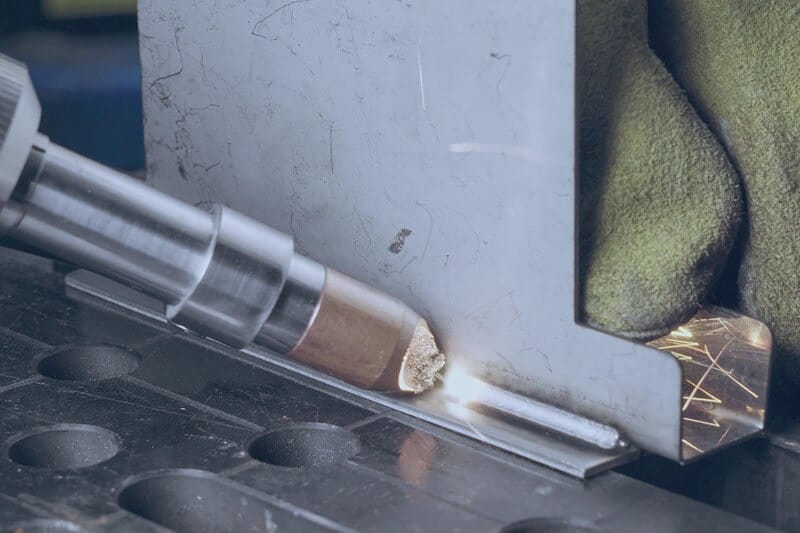
Conduction welding is suitable for thin-walled metals and applications where a shallow weld depth is required. The heat from the laser is conducted into the metal, causing it to melt and form a weld. Keyhole welding, on the other hand, is used for thicker metals. The high-energy laser beam creates a keyhole in the metal, which is filled with molten metal as the laser moves along the joint.
Laser welding offers several advantages, such as high welding speed, low heat-affected zone, and the ability to weld dissimilar metals. It also produces strong and aesthetically pleasing welds, making it ideal for applications in industries where both strength and appearance are important.
4. Laser Cleaning
Laser cleaning is a non-contact, environmentally friendly method for removing contaminants from metal surfaces. The process works by directing a laser beam onto the metal surface. The laser energy is absorbed by the contaminants, such as rust, paint, or grease, causing them to vaporize or break away from the metal surface.
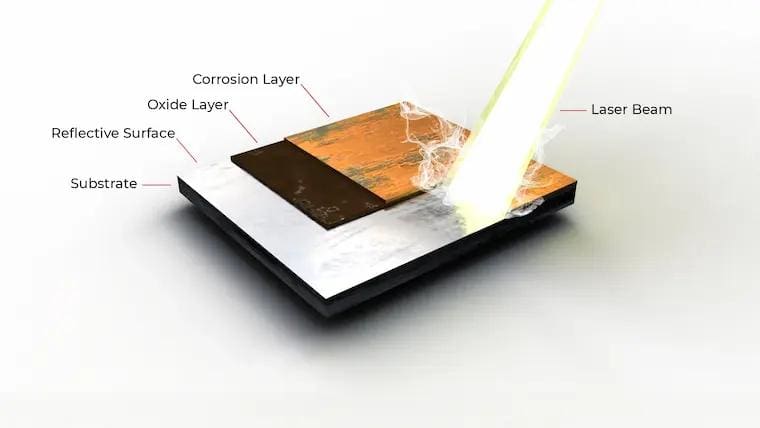
The advantage of laser cleaning is that it can be highly selective, removing only the contaminants without damaging the underlying metal. It is also a dry process, which means there is no need for chemicals or water, reducing waste and environmental impact. Laser cleaning can be used for a variety of applications, from restoring historical metal artifacts to preparing metal surfaces for painting or welding.