Laser cleaning principle
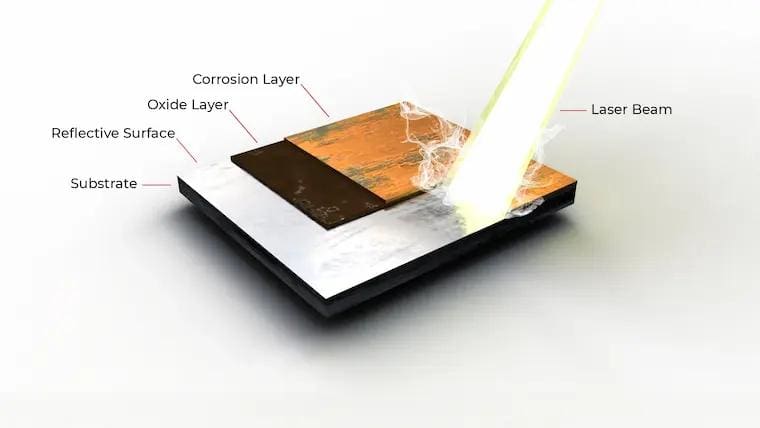
The principle of laser cleaning is to use the difference in the laser absorption coefficient of a specific wavelength between the cleaning substrate and pollutants, or the difference in physical parameters such as the melting point, boiling point, thermal expansion coefficient, etc. of the two. After the pollutants absorb laser energy, they are vaporized and evaporated, vibrated and peeled off, and ultimately peeled off the surface of the substrate to achieve the purpose of cleaning. The metal substrate reflects most of the laser after the pollutants are removed, and the cleaning process has almost no damage to the substrate.
- Accurate cleaning
- Clean visible dirt
- No consumables
- Non-contact
- Environmental
- Undamage
Traditional cleaning methods
Chemical cleaning
- Environmental pollution
- Consumable materials
Mechanical cleaning
- Low cleanliness
- Injury serious
- High labor intensity
- Poor consistency
Ultrasonic cleaning
- Size limited
- Unstable quality
- Consumables
Laser Cleaning
Technical advantages
- Controllable cleaning area and cleaning thickness
- Uniform and consistent
- Convenient detection and control, process intelligentization
- No damage only clean surface pollutant
- Non-contact handheld and automated
Social and economic advantages
- Environmental protection and low noise
- Easy maintenance, and no vulnerable parts
- Runs with low cost, low electricity consumption (Hundred watts - thousand watts)
- No consumables, and low electricity consumption
- Reduce labor force and labor costs
Comparison of Cleaning Effect Details

We are dedicated to offering laser cleaning machines to a diverse range of industries, including but not limited to aerospace, rail transit, automotive manufacturing, the nuclear industry, engineering machinery, and shipbuilding – all of which are integral components of the heavy – industrial sector.
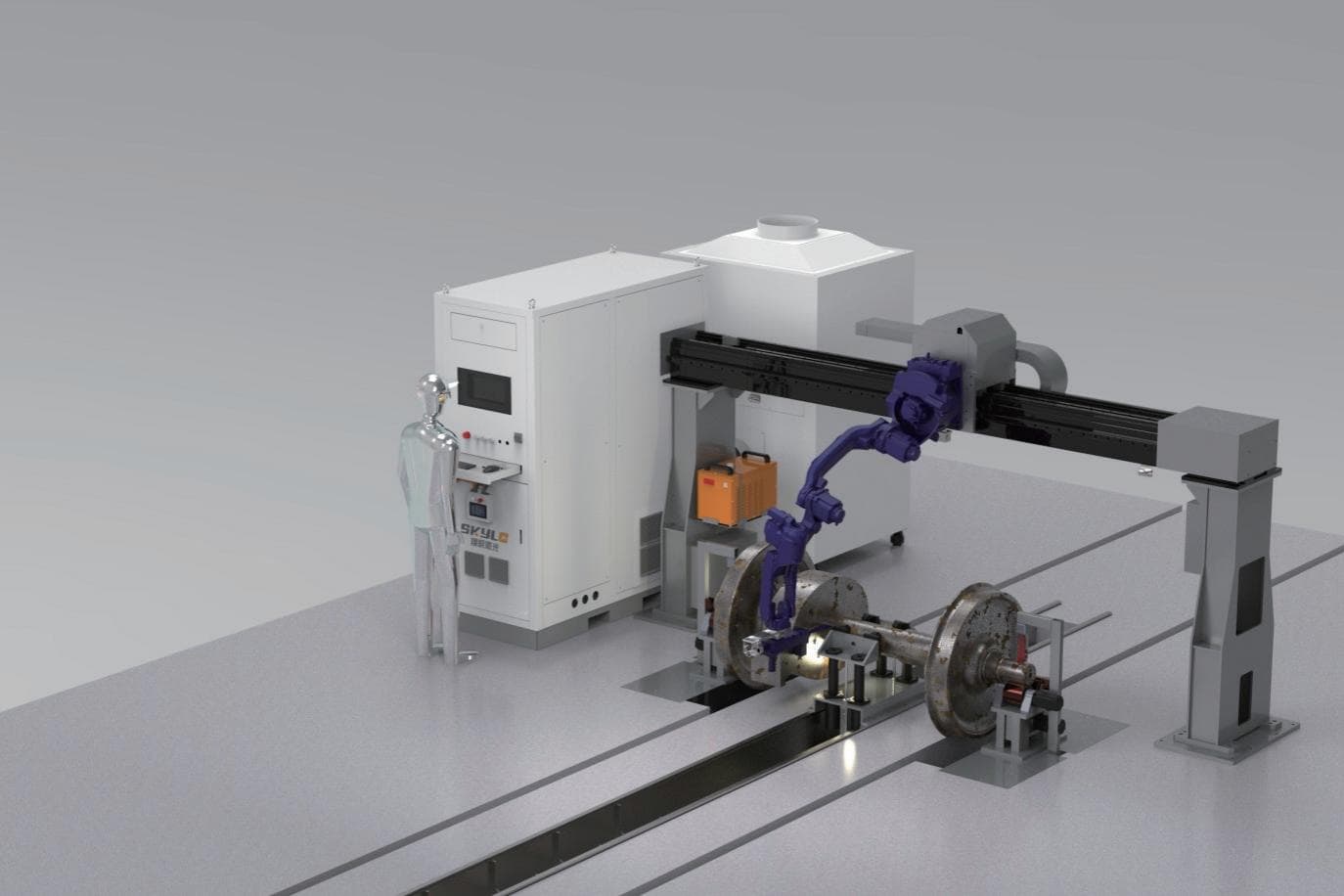