The four most important parameters in control Layout:
- LASER POWER
- LASER FREQUENCY
- LASER PULSE WIDTH
- MIRROR FREQUENCY
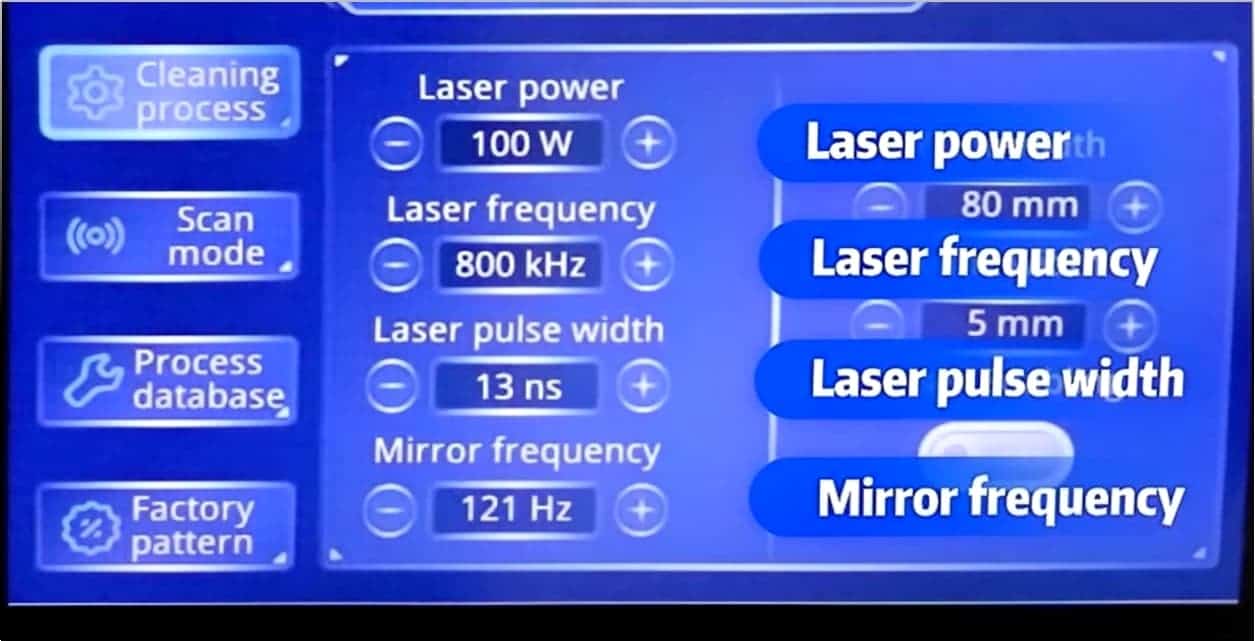
1. LASER POWER
Laser power is a crucial parameter that determines the energy intensity of the laser beam. In pulse laser cleaning, higher laser power means more energy is delivered to the surface of the object being cleaned per unit time. This enables the laser to more effectively break the bonds between dirt, rust, coatings and the substrate material, facilitating their removal. For example, when dealing with thick and tough rust layers on metal surfaces, a higher laser power is often required to ensure thorough cleaning. However, if the power is too high, it may cause damage to the substrate surface, such as melting or deforming. Therefore, appropriate laser power needs to be selected according to the specific cleaning requirements and the characteristics of the material.
2. LASER FREQUENCY
Laser frequency refers to the number of laser pulses emitted per second. It affects the cleaning efficiency and the quality of the cleaning surface. A higher laser frequency means more laser pulses act on the surface within a certain period, which can improve the cleaning speed and make the cleaning effect more uniform. For instance, in the cleaning of large – area surfaces, a higher frequency can help to cover the surface more quickly and evenly, reducing the cleaning time. On the other hand, if the frequency is too high, it may lead to excessive heat accumulation on the surface, which is not conducive to precise cleaning and may also affect the performance of the laser device itself.
3. LASER PULSE WIDTH
Laser pulse width is the duration of each laser pulse. It has a significant impact on the interaction between the laser and the material surface. A longer pulse width means that the laser energy is applied to the surface for a longer time, which can increase the energy absorption of the dirt and impurities on the surface, making it easier to remove them. But at the same time, a longer pulse width also means more heat is transferred to the substrate, which may cause thermal damage to the substrate material. In the case of cleaning delicate materials or requiring high – precision cleaning, a shorter pulse width is usually chosen to minimize thermal effects and ensure the integrity of the substrate surface.
4. MIRROR FREQUENCY
The mirror frequency mainly affects the scanning speed and accuracy of the laser beam. The galvanometer scanner controls the direction of the laser beam by adjusting the angle of the mirror. A higher mirror frequency allows the laser beam to scan the surface more quickly and accurately, enabling more precise control of the cleaning area and path. This is particularly important in complex – shaped surface cleaning or when high – precision cleaning is required. For example, in the cleaning of microelectronic components or the detailed parts of precision machinery, a high mirror frequency can ensure that the laser beam accurately acts on the target area without affecting the surrounding areas, improving the cleaning quality and precision.
PULSE LASER CLEANING TEST
The following are the differences in the effects on the same material under the same power and different parameters.

Pulse Laser Cleaning Test 01 - Paper
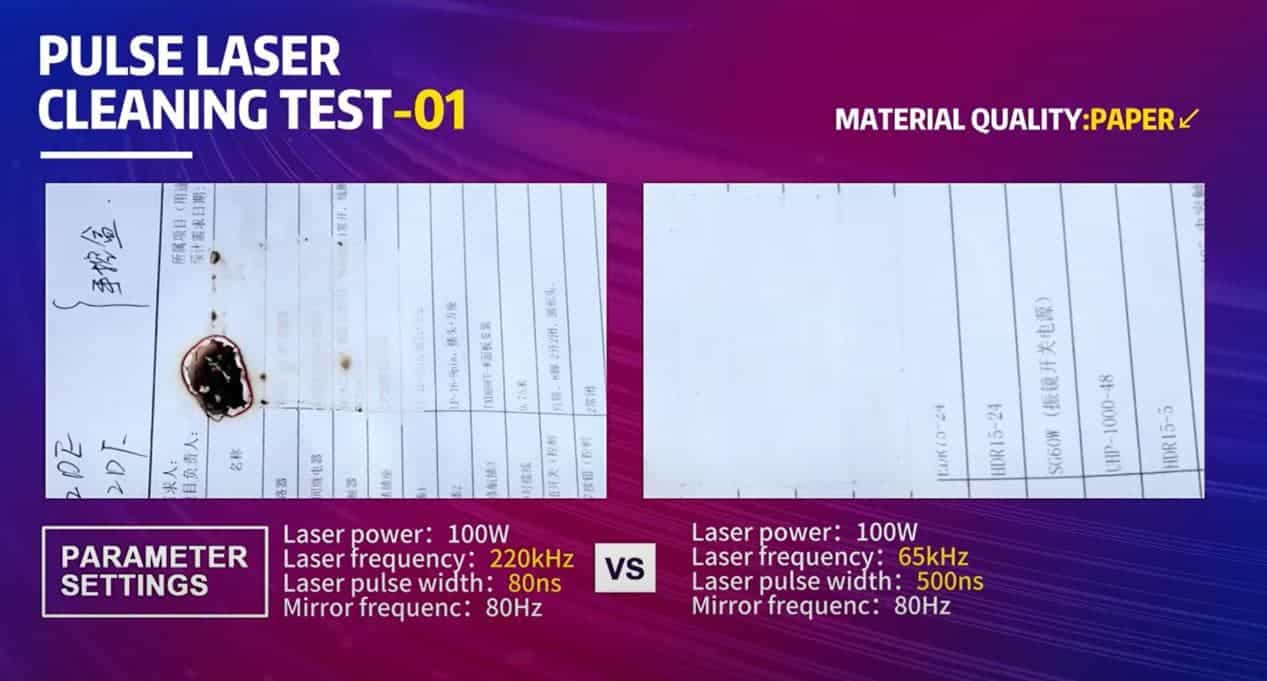
Pulse Laser Cleaning Test 02 - Wood
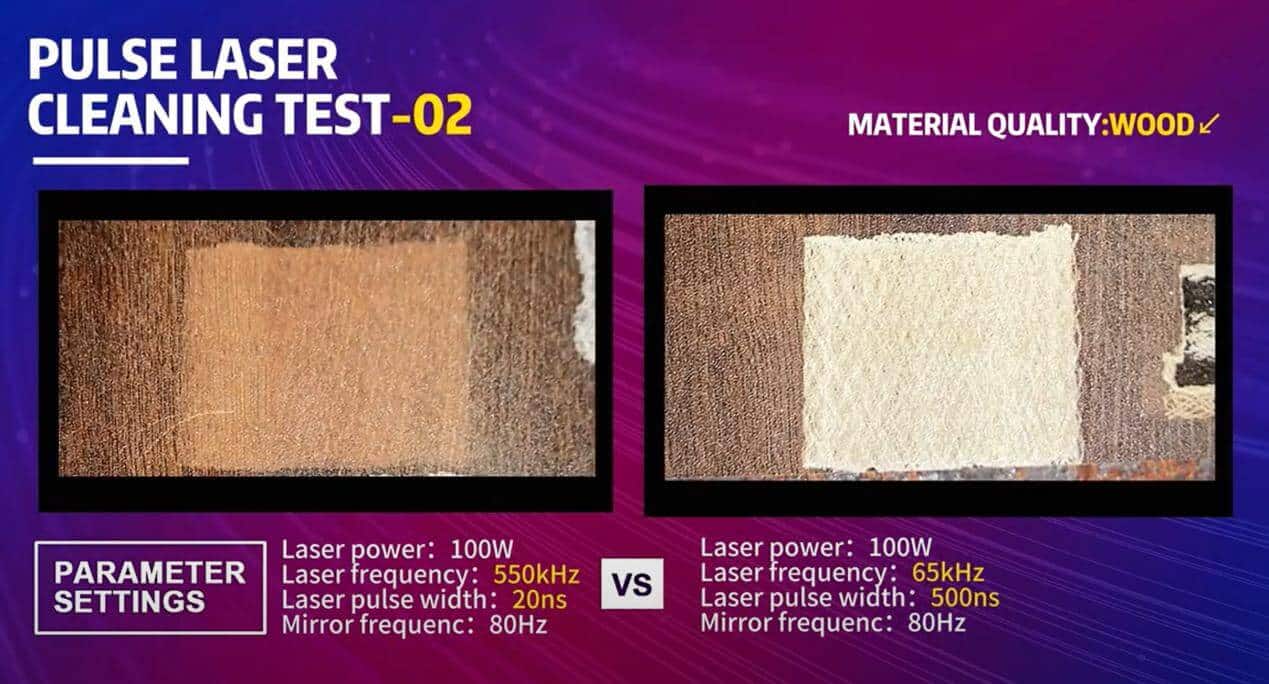
Pulse Laser Cleaning Test 03 - SUS
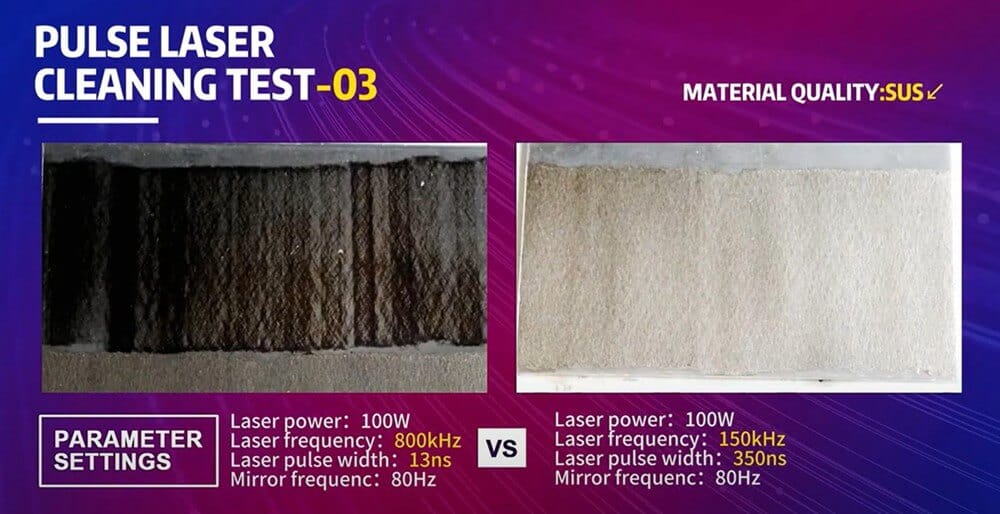
Pulse Laser Cleaning Test 04 - Coating
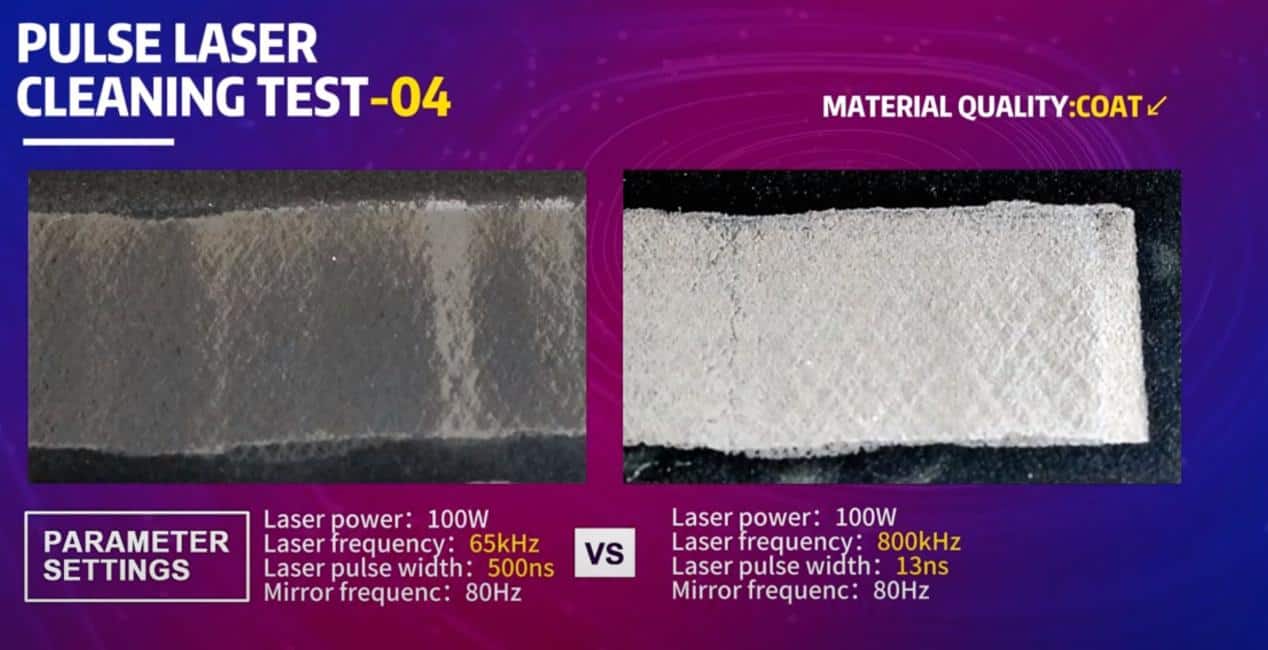
Pulse Laser Cleaning Test 05 - Rust
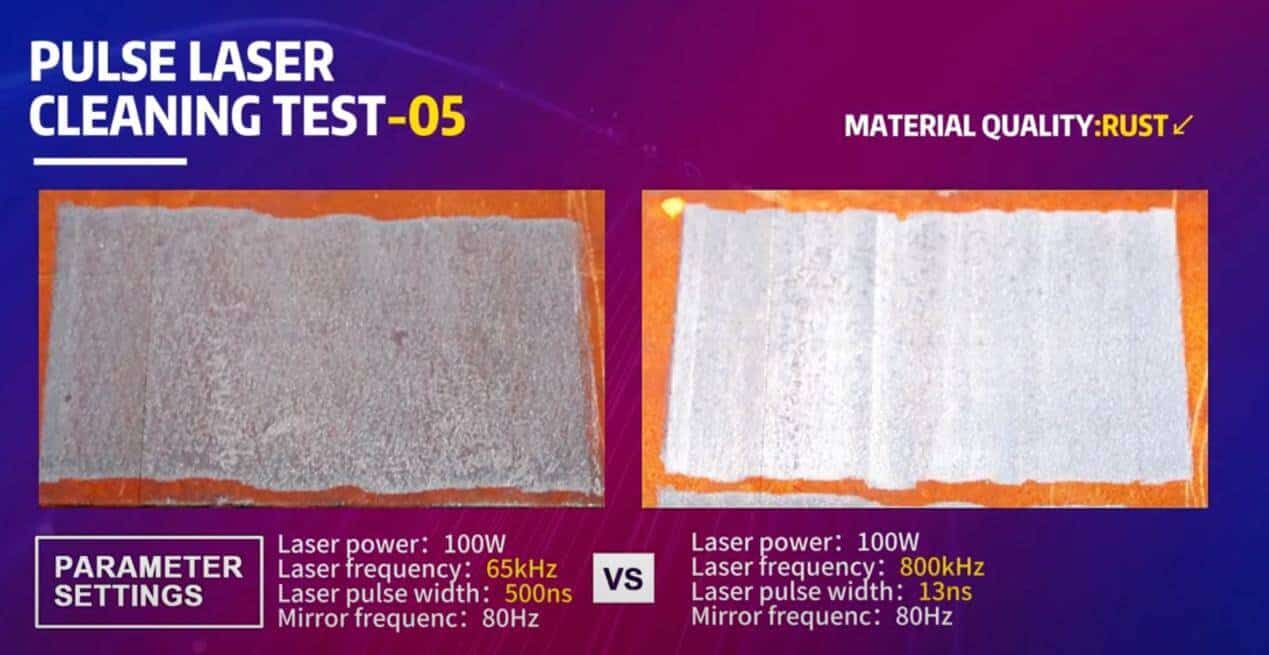
What are the advantages of Redshift Laser Cleaning Machines?
- Spearhead the formulation of the first national standard for laser cleaning, thereby filling the void in the standards of the cleaning industry.
- Demonstrate technological leadership by independently researching and developing laser cleaning control systems and external optical devices with complete independent intellectual property rights.
- Manufacture a number of industry-specific products with high-level technical barriers, such as fully-automatic laser cleaning equipment based on machine vision and laser welding-cleaning synchronous equipment.
- The Redshift laser cleaning machine is capable of long-term and stable operation under harsh environmental conditions including temperature variations, humidity, smoke, and dust.