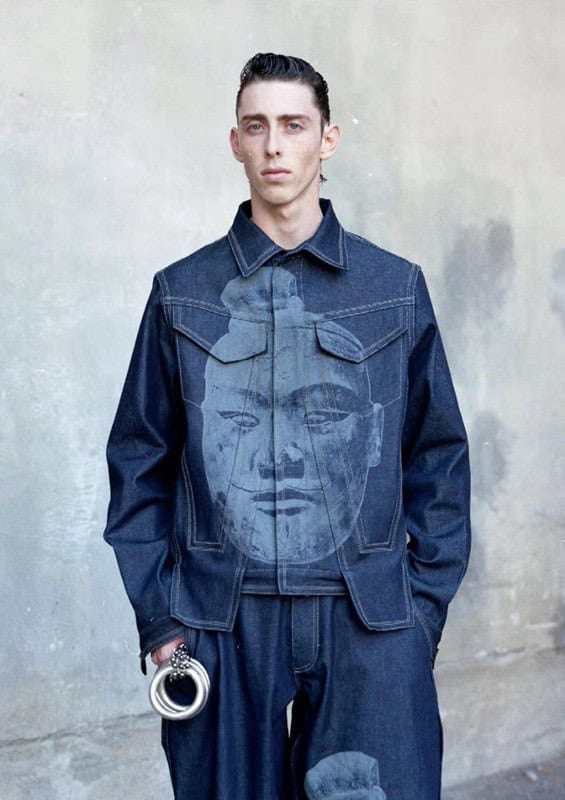
1. The Principle of 3D Galvo Laser
3D Galvo laser, short for 3-Dimensional Galvanometer-scanning laser, is a high-tech laser processing technology. It mainly consists of a laser source, a galvanometer scanning system, and a focusing system.
The laser source generates a high-energy laser beam. The galvanometer scanning system is the core component that enables the high-speed movement of the laser beam. It contains two high-speed rotating galvanometer mirrors, one for the X-axis and the other for the Y-axis. By controlling the deflection angles of these two mirrors, the laser beam can be rapidly scanned within a certain two-dimensional plane.
The focusing system then focuses the scanned laser beam onto the target surface. In the case of 3D processing, an additional Z-axis control mechanism is added. This allows for the adjustment of the focal length according to the height or depth of the object, enabling the laser to process objects with complex three-dimensional shapes accurately. The entire system is highly automated and can be precisely controlled by computer-aided design (CAD) and computer-aided manufacturing (CAM) software, which enables the realization of highly customized and complex processing tasks.
2. Reasons for Replacing Traditional Chemical Denim Washing with Laser
Environmental Protection
Traditional chemical denim washing involves the use of a large amount of water, various chemical agents such as pumice stones, enzymes, and bleaching agents. These chemicals not only pollute water sources but also release harmful substances into the environment during the washing process. In contrast, laser washing is a dry – processing method that does not require water or chemical additives. It significantly reduces wastewater discharge and environmental pollution, making it a more sustainable option for the denim industry.
Cost - effectiveness
Although the initial investment in laser equipment is relatively high, in the long run, laser washing can save costs. Traditional chemical washing requires continuous consumption of water, chemicals, and pumice stones, and also involves high costs for wastewater treatment. Laser washing eliminates the need for these consumables and reduces the cost of wastewater treatment. Moreover, the high – efficiency processing of laser can improve production speed, which also helps to reduce overall production costs.
Design Flexibility
Traditional chemical washing methods are limited in creating complex and precise patterns on denim. Laser technology, on the other hand, can be accurately controlled by software. It can create a wide variety of patterns, from simple fading effects to extremely intricate geometric patterns and personalized designs. This provides denim manufacturers with greater design flexibility to meet the diverse needs of the market.
3. The Process of Denim Laser Washing
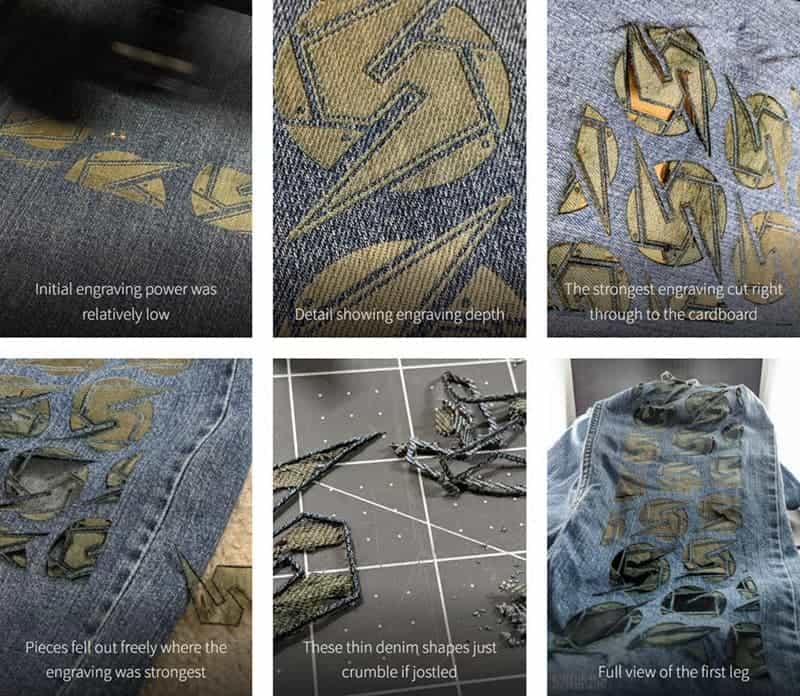
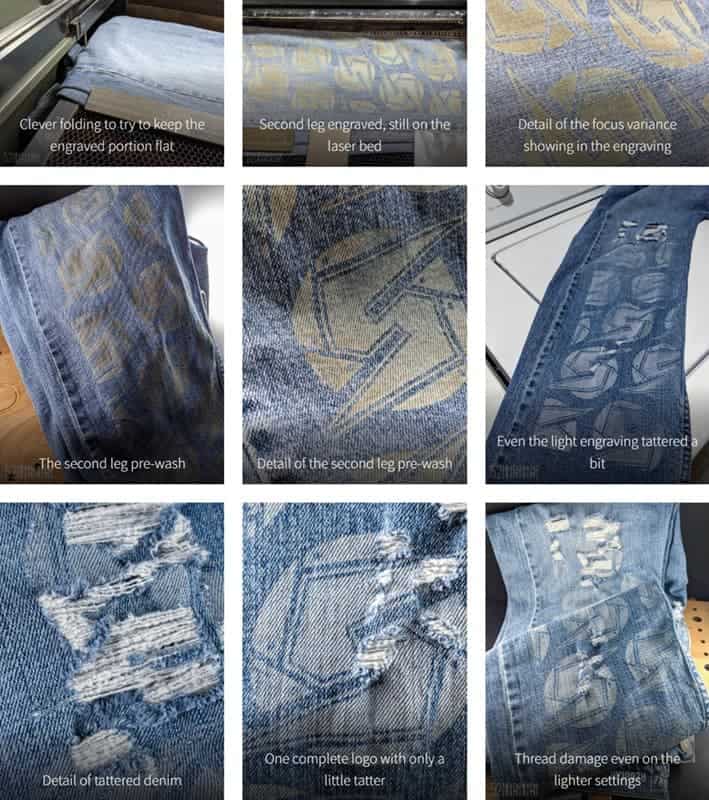
Pre-treatment
Before laser washing, the denim fabric needs to be pre-treated. This mainly includes cleaning the fabric to remove any impurities, oils, or sizing agents on the surface, which could affect the laser – processing effect. The fabric is also usually fixed on a special workbench or fixture to ensure stable processing during the laser – washing process.
Laser washing operation
The pre-treated denim is then placed under the 3D Galvo CO2 laser. The operator sets relevant parameters in the control software according to the desired washing effect, such as laser power, scanning speed, and scanning pattern. The laser beam is scanned onto the denim surface according to the set program. When the laser beam hits the denim, it vaporizes the dye on the fabric surface, achieving a fading or pattern-forming effect. For example, a lower laser power with a higher scanning speed can create a light-fading effect, similar to a light-wash denim look. Higher laser power and slower scanning speed can be used to create deeper fading or more distinct patterns.
Post-treatment
After laser washing, the denim may need post-treatment. This may include a simple cleaning process to remove any remaining debris or vaporized dye particles. In some cases, a softening treatment may also be carried out to ensure that the denim still has a good hand-feel and wearing comfort.
4. Application Cases of Denim Laser Washing
Levi's
Levi’s, a well-known denim brand, has adopted laser washing technology in some of its product lines. By using 3D Galvo CO2 laser, they have been able to create unique and eye-catching patterns on their denim products. For example, in a special limited-edition series, laser-washing was used to create intricate floral patterns on the denim surface. This not only added a new aesthetic element to the traditional denim but also received positive feedback from consumers for its environmental-friendly production process. The brand also found that the use of laser washing technology improved production efficiency and reduced production costs in the long-term operation.
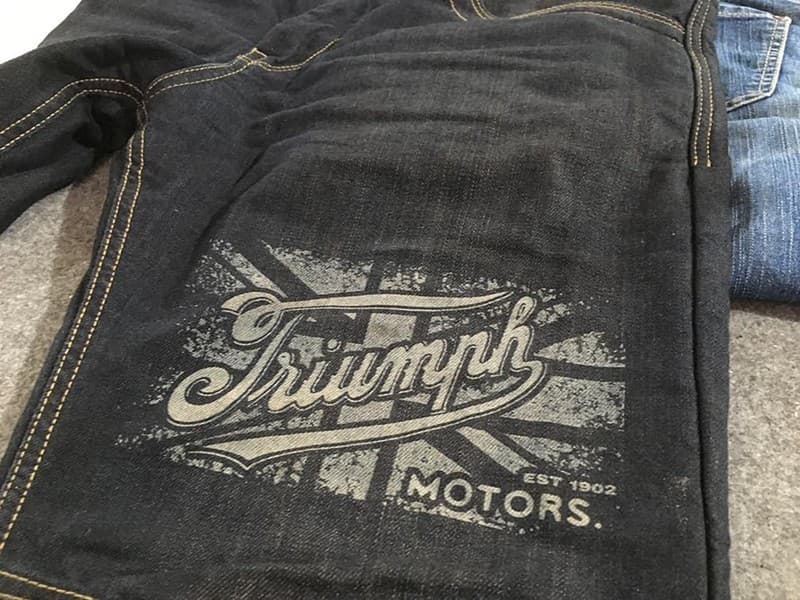
Wrangler
Wrangler has applied laser washing technology to create a more natural and unique fading effect on its denim jeans. Through precise control of the laser parameters, they can simulate the effect of long-term natural wear and washing on denim. This new fading effect has become a selling point of their products, attracting consumers who pursue a more authentic and personalized denim look. In addition, Wrangler also reduced its environmental footprint by replacing traditional chemical washing with laser washing technology, which is in line with the current trend of sustainable development in the fashion industry.
How do the process parameters of denim laser washing affect the washing effect?
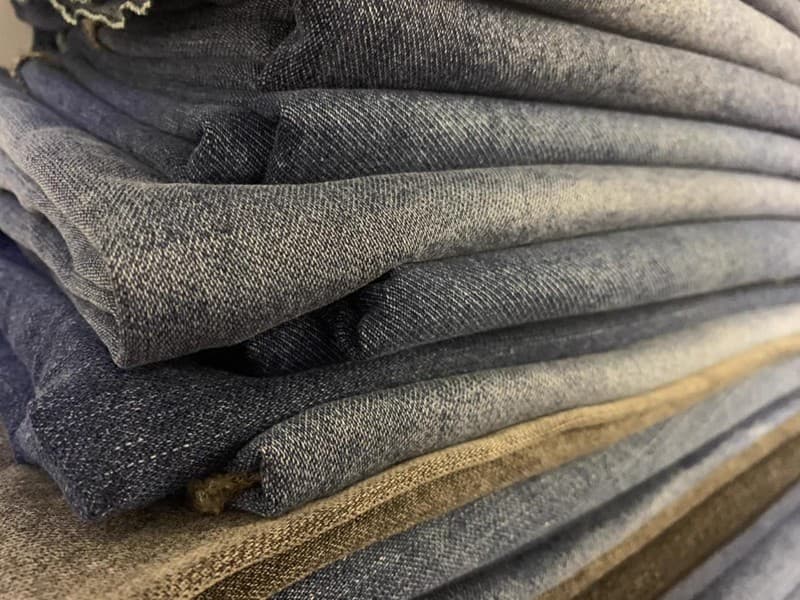
The process parameters of denim laser washing mainly include laser power, scanning speed, pulse frequency, spot diameter, and defocus amount. These parameters play a crucial role in determining the washing effect. The following is a detailed introduction for you:
Laser power
Degree of fading: The laser power directly determines the amount of energy acting on the denim fabric. The higher the power, the greater the instantaneous energy generated, which can more effectively decompose and vaporize the dyes on the denim fabric, resulting in a deeper fading effect. For example, if you want to create a heavily faded effect similar to that of denim after long – term wear and multiple washes, you can appropriately increase the laser power. Conversely, a lower power can only cause slight decomposition of the dyes, resulting in a shallower degree of fading, which is suitable for a light-wash effect.
Degree of ablation: Excessively high laser power may cause excessive ablation on the fabric surface, leading to fabric damage, hardening, or even perforation. This not only affects the aesthetic appearance of the denim but also reduces its durability and wearing comfort. An appropriate power can achieve the desired fading effect while ensuring the integrity and original texture of the fabric.
Scanning speed
Uniformity: The scanning speed affects the duration of the laser’s action on the denim fabric. If the speed is too fast, the laser acts for a short time, and the energy received by each part of the fabric is insufficient and uneven. This may result in inconsistent fading effects, with patches of different colors. A slower scanning speed allows the laser to act on the fabric more uniformly, achieving a more even fading effect and making the washed appearance more natural.
Depth of fading: The scanning speed is inversely proportional to the depth of fading. The slower the speed, the longer the laser acts on a unit area, and the more energy is transferred, resulting in deeper fading. Conversely, a faster scanning speed leads to shallower fading.
Pulse frequency
Pattern fineness: The pulse frequency determines the emission interval of laser pulses. A higher pulse frequency means more laser pulses are emitted per unit time, which can form denser action points on the fabric, thus achieving finer patterns and more delicate texture effects. For example, for some complex patterns or intricate designs, a high – pulse frequency can ensure the clarity and integrity of the pattern.
Continuity of the fading effect: An appropriate pulse frequency can ensure the continuity and smoothness of the fading effect. If the pulse frequency is too low, the fading effect may be intermittent, resulting in discontinuous spots or stripes that affect the overall visual effect.
Spot diameter
Pattern size and clarity: The spot diameter determines the area of the fabric on which the laser acts. A larger spot diameter is suitable for large-area fading or simple large-scale patterns, as it can quickly cover a large area, but the pattern’s detail-expression ability is relatively weak. A smaller spot diameter is more suitable for creating fine small patterns and complex details, enabling higher pattern accuracy and clarity, but the efficiency is lower when processing large areas.
Edge effect: The spot diameter also affects the clarity and transition effect of the pattern edges. A smaller spot results in sharper and clearer edges when cutting or engraving patterns, while a larger spot may cause a certain degree of blurring and transition at the edges, making the pattern look softer.
Defocus amount
Depth and range of fading: The defocus amount refers to the relative position of the laser focus and the fabric surface. When the defocus amount is positive, the focus is above the fabric, and the laser energy is more dispersed on the fabric surface. The fading range is larger but the depth is shallower, which is suitable for large – area light – fading treatment. When the defocus amount is negative, the focus is below the fabric, and the laser energy is more concentrated on the fabric surface. The fading depth increases, but the range is relatively smaller, which can be used for local deep fading or highlighting specific patterns.
Degree of fabric damage: An appropriate defocus amount can reduce damage to the fabric while achieving the desired washing effect. If the defocus amount is inappropriate, it may cause local overheating of the fabric, resulting in excessive ablation or damage, which affects the quality and appearance of the denim.