1. Automotive Industry
In the automotive industry, laser technology has been a game-changer, driving a series of revolutionary transformations when compared to traditional metal-processing modes.
Laser Cutting
When it comes to car body component production, laser cutting stands out with its high-precision capabilities. Traditional stamping techniques rely on expensive molds. For instance, creating a set of molds for a new car model can cost hundreds of thousands or even millions of dollars. Moreover, any design changes during the production process are extremely time-consuming and costly. A simple adjustment to the shape of a car door panel might require the redesign and remanufacture of the corresponding mold, which could take weeks or even months and incur substantial expenses.
On the contrary, laser cutting offers a more flexible and efficient solution. It enables rapid prototyping. Automotive designers can quickly transform their concepts into physical parts. They can cut complex shapes directly from metal sheets, eliminating the need for multiple manufacturing steps. For example, a complexly curved fender can be precisely cut by a laser in one operation, while traditional methods might involve multiple stamping and machining processes. This not only shortens the production cycle but also reduces the overall cost of production.
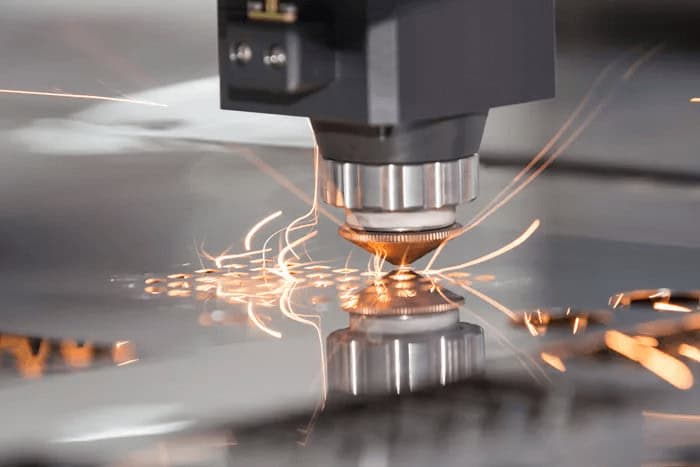
Laser Welding
Laser welding has also become an indispensable part of automotive manufacturing. Modern car bodies commonly use a combination of different metals, such as steel and aluminum, to achieve a balance between strength and weight. Laser welding excels in joining these dissimilar metals. It can create high-strength welds, which significantly improve the overall safety and durability of the vehicle. The precise control of the laser beam allows for a narrow and deep weld, minimizing the heat-affected zone.
In contrast, traditional welding methods, like arc welding, often struggle when it comes to joining dissimilar metals. They may produce larger heat-affected zones, which can lead to a reduction in the strength and ductility of the metal. For example, in arc welding of steel and aluminum joints, the large heat input can cause the formation of brittle intermetallic compounds at the interface, weakening the joint and potentially compromising the safety of the vehicle.
2. Steel Structure Industry
In the steel structure industry, laser cutting has brought about a revolutionary change in the production of steel components.
Precision and Quality
Traditional cutting methods in the steel structure industry, such as oxy-fuel cutting or plasma cutting, often result in rough edges and significant dimensional errors. Oxy-fuel cutting, for example, can leave a thick layer of dross on the cut surface, which requires additional grinding and finishing processes. Plasma cutting may also cause some distortion and unevenness in the cut edges.
Laser cutting, on the other hand, offers exceptional precision. It can achieve very narrow kerf widths, typically in the range of 0.1-0.3 mm, compared to several millimeters for traditional methods. This high precision ensures that the steel components fit together perfectly during assembly, reducing the need for on – site adjustments and improving the overall quality of the steel structure. For large-scale steel bridges or high-rise buildings, the accurate fit of components is crucial for the structural integrity and safety of the entire project.
Design Flexibility
Traditional cutting methods are often limited in terms of the complexity of shapes they can cut. They are more suitable for simple geometric shapes like straight lines and circles. When it comes to cutting intricate patterns or non-standard shapes, the cost and difficulty increase significantly.
Laser cutting provides unparalleled design flexibility. It can cut any shape programmed into the control system, whether it is a complex decorative pattern on a steel facade or a custom-designed bracket for a special-purpose steel structure. This allows architects and engineers to unleash their creativity and design more innovative and aesthetically pleasing steel structures.
Productivity and Cost-effectiveness
In terms of productivity, laser cutting is much faster than traditional methods, especially for small-to-medium-sized steel components. The non-contact nature of laser cutting means there is no tool wear, and the cutting speed can be adjusted according to the thickness and type of steel. This results in a higher production rate and shorter lead times.
Although the initial investment in laser cutting equipment is relatively high, in the long run, it can be more cost-effective. The reduction in post-processing steps, such as grinding and finishing, and the higher material utilization rate due to the narrow kerf width contribute to overall cost savings. Additionally, the ability to quickly adapt to design changes and produce customized components gives steel structure manufacturers a competitive edge in the market.
3. Metal-processing Industry
In the general metal-processing industry, laser technology has also made a profound impact and brought about significant transformations compared to traditional metal-processing modes.
Laser Marking
In the metal-processing industry, product identification and traceability are crucial. Traditional marking methods, such as stamping or engraving with mechanical tools, have several limitations. Stamping can cause deformation of the metal surface, especially for thin-walled or delicate parts. Mechanical engraving is a slow process and may not be suitable for high-volume production.
Laser marking offers a non-contact, high-speed, and permanent marking solution. It can mark various types of information, such as serial numbers, barcodes, logos, and part numbers, on metal surfaces with high precision. The laser-marked information is clear, durable, and resistant to wear, corrosion, and environmental factors. This is particularly important for industries where product traceability is required, such as aerospace and medical device manufacturing.
Laser Cleaning
Laser cleaning has emerged as an alternative to traditional chemical and mechanical cleaning methods in the metal-processing industry. Traditional cleaning methods often involve the use of harsh chemicals, which can be harmful to the environment and human health. They may also cause damage to the metal surface, such as pitting or corrosion.
Laser cleaning is a non-contact, environmentally friendly method. It uses high-energy laser pulses to remove contaminants, such as rust, paint, and grease, from the metal surface. The laser energy can be precisely controlled to selectively remove the contaminants without damaging the underlying metal. This makes it suitable for a wide range of applications, from restoring historical metal artifacts to preparing metal surfaces for painting or welding.
In conclusion, laser applications in the metal industry have brought about significant improvements in precision, flexibility, productivity, and environmental friendliness compared to traditional metal – processing modes. As laser technology continues to evolve, its impact on the metal industry is expected to grow even further.