In the garment manufacturing industry, traditional manual cutting and mechanical blade – cutting are gradually being replaced by a “non – contact” high – tech process: CO2 laser cutting machines. This technology can not only accurately cut complex patterns but also avoid problems such as fabric deformation and fraying edges. It can be regarded as the “precision scalpel” in garment manufacturing. This article will deeply analyze its working principle, applicable fabric types, operation skills, and reveal how to achieve efficient production through parameter optimization.
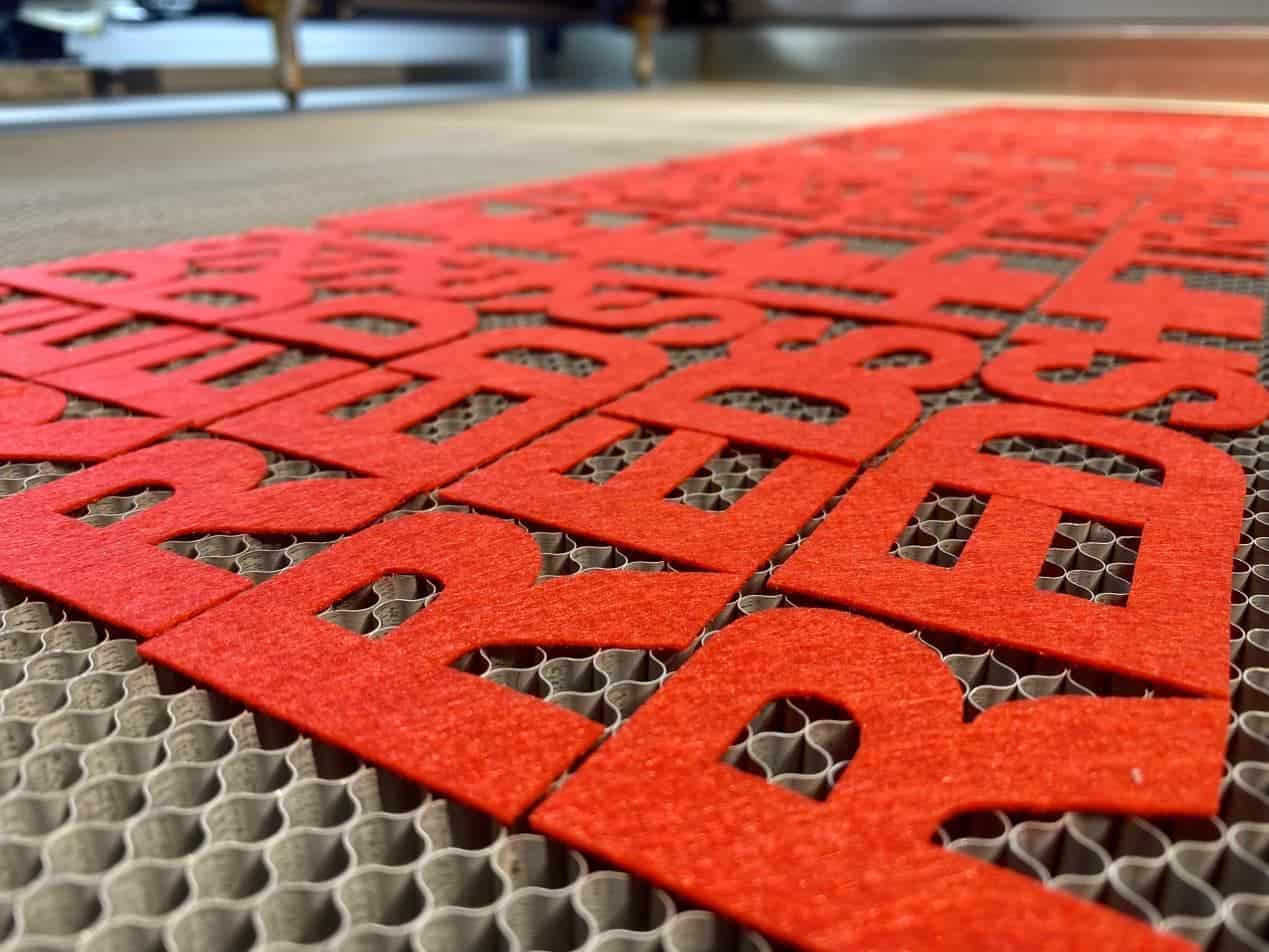
I. The Core Principle of CO2 Laser Cutting
CO2 laser cutting machines generate infrared laser with a wavelength of 10.6 micrometers through the ionization of carbon dioxide gas. Lasers of this wavelength have high absorbability, especially suitable for processing garment fabrics containing cellulose (such as cotton and linen) and synthetic fibers (such as polyester and nylon).
The laser beam is converged into a high – energy light spot with a diameter of 0.1 – 0.3 mm by a focusing lens, and the local area of the fabric is instantly heated to the vaporization temperature (about 300 – 500°C), forming a cutting seam through “vaporization – ablation”. Since it is a non – contact processing method and does not require physical pressure, it can avoid fabric stretching and deformation, especially suitable for handling light, thin, and elastic materials.
II. Classification of Applicable Fabrics and Parameter Optimization
The fiber composition and structure of different fabrics vary significantly, and laser parameters need to be adjusted accordingly. The following are the cutting key points for common fabrics:
Fabric Type | Characteristics | Recommended Parameters (Power/Speed/ Air Pressure) | Notes |
Cotton/Linen | Flammable and prone to carbonization | Low power (30 – 60W), high speed (3 – 5m/min), medium air pressure (0.8 – 1.2Bar) | Install auxiliary air – blowing to prevent edge charring |
Polyester/Nylon | Low melting point and prone to melting and sticking | Medium power (60 – 100W), medium speed (2 – 3m/min), high air pressure (1.5 – 2Bar) | It is necessary to quickly blow away the molten matter to avoid caking |
Silk/Chiffon | Light, thin, and prone to heat damage | Ultra – low power (20 – 40W), ultra – high speed (5 – 8m/min), low air pressure (0.5Bar) | Use the pulse mode to reduce heat accumulation |
Composite Fabrics | Multi – layer structure and complex composition | Test parameters layer by layer and cut step by step | Avoid incomplete cutting of the bottom layer or over – burning of the surface layer |
Key Skills:
- Test – cutting Verification: Test with scraps and observe whether the cut is smooth and whether there is carbonization.
- Layer – by – layer Cutting: For multi – layer composite fabrics, the surface layer can be cut at low power first, and then the power can be increased to cut the bottom layer.
III. Four Process Skills for Improving Cutting Quality
1. Focus Position Calibration
The focus position directly affects the cutting accuracy. For fabrics with a thickness of ≤3mm, it is recommended to place the focus on the material surface; when it exceeds 3mm, the focus can be appropriately moved down (such as 0.5mm) to enhance the penetration ability. Detection Method: Tilt the cutting test piece and observe the consistency of the cut width.
2. Air Pressure and Auxiliary Gas Selection
- Compressed Air: Economical and general – purpose, suitable for most synthetic fibers, with the air pressure controlled at 1 – 2Bar.
- Nitrogen: Inert gas can reduce the oxidation reaction and avoid the blackening of the edges of natural fibers, but the cost is high.
3. Layout Optimization and Material Utilization
Use CAD software for automatic nesting layout to reduce waste materials at the corners. For example, when cutting lace edges, the “mirror – symmetry” layout can save 15% – 20% of materials. For elastic fabrics, a thermal shrinkage compensation amount of 0.1 – 0.3mm should be reserved.
4. Maintenance and Safety
- Clean the lenses and mirrors daily to prevent smoke and dust from adhering and reducing the laser efficiency.
- Install a smoke – exhaust system to avoid harmful gases (such as cyanides generated when cutting chemical fibers) from harming the operators.
IV. The Unique Advantages and Limitations of Laser Cutting
Advantages:
- One – step Formation of Complex Patterns: It can cut out hollow patterns and curved edges, which traditional knife molds cannot achieve.
- Non – contact and Zero Pollution: No molds are required, reducing tool wear and material waste.
- Edge – sealing Effect: The high temperature of the laser can instantly melt the edges of chemical fiber fabrics, achieving “automatic edge – sealing” and eliminating subsequent processing.
Limitations:
- Easy Carbonization of Natural Fibers: For materials such as cotton and linen, the power needs to be strictly controlled; otherwise, the edges will turn yellow.
- Thickness Limitation: The thickness of the fabric cut at one time is generally not more than 10mm. If it is too thick, multiple processing is required.
V. Future Trends: Intelligence and Green
- AI – based Parameter Adaptation: Real – time monitoring of cutting quality through cameras, and automatic adjustment of power and speed by AI algorithms.
- Environmental Upgrade: Research and development of low – energy – consumption lasers, and the matching of special cutting modes for biodegradable fabrics.
- 3D Laser Cutting: Combining 3D scanning technology to directly cut three – dimensional garment patterns according to human body model data.
Conclusion
CO2 laser cutting machines are redefining the boundaries of precision and efficiency in garment manufacturing. Mastering the balance between fabric characteristics and parameter optimization can not only improve product quality but also promote the industry’s development towards flexibility and sustainability. In the future, with the iteration of technology, this “blade of light” may become a standard tool in every garment factory.